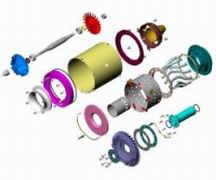 |
First off, here are the parts I need. I know it's rather small so you can click on it to enlarge it.
|
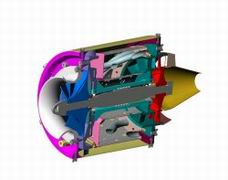 |
And this is how it fits together. (no large picture yet)
|
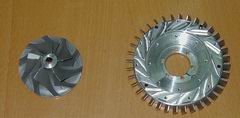 |
O.k. Let's start with the parts I bought.
Here we have the compressor and the diffuser.
The compressor is a stock Allied Signal/Garrett compressor (446335-10). It's surprisingly small
(everything on this engine is) and made of aluminum. It came re-profiled and balanced.
The diffuser is a real jewel. It's a CNC milled aluminum part that is really complex.
I could have made it myself but my guess is that doing it would have taken me the better part of this century.
|
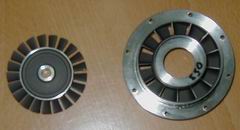 |
Here's the turbine and the NGV.
The turbine is cast out of Inconel 714c and is really neat just to look at. I bought the machined
turbine for two reasons: 1) Buying the drill and reamer needed to complete the turbine would have
cost more than the difference, 2) I don't think that I want my first boring and reaming experience to
be on a really expensive part that's made of a really tough metal.
The NGV (Nozzle Guide Vanes) is cast out of Stainless Steel and is also a wonderful lost-wax cast.
As you can probably see, I bought this part machined as well. The reasons are that I thought that machining it
would be difficult and that I probably would mess it up (again, not something you want to do with an expensive part).
As I see it, I saved a fortune on broken taps.
|
 |
Here's the combustion chamber (combustor).
Now you may think I'm just lazy and that I could have saved quite a bit of money on buying the parts and
constructing this myself. You may be right. But looking at the work Wren did here I'm not sure I could
have spot welded this together so well. It's really accurate and solid. It's fun just looking at it.
|
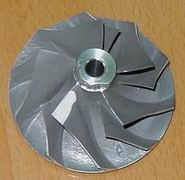 |
Here's a close-up of the compressor showing the result of the balancing process.
Quite a bit of material taken out of the hub.
|
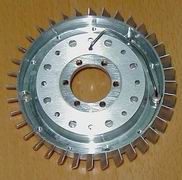 |
Rear shot of the diffuser. You can also see the filter ring and lubrication feed line.
|